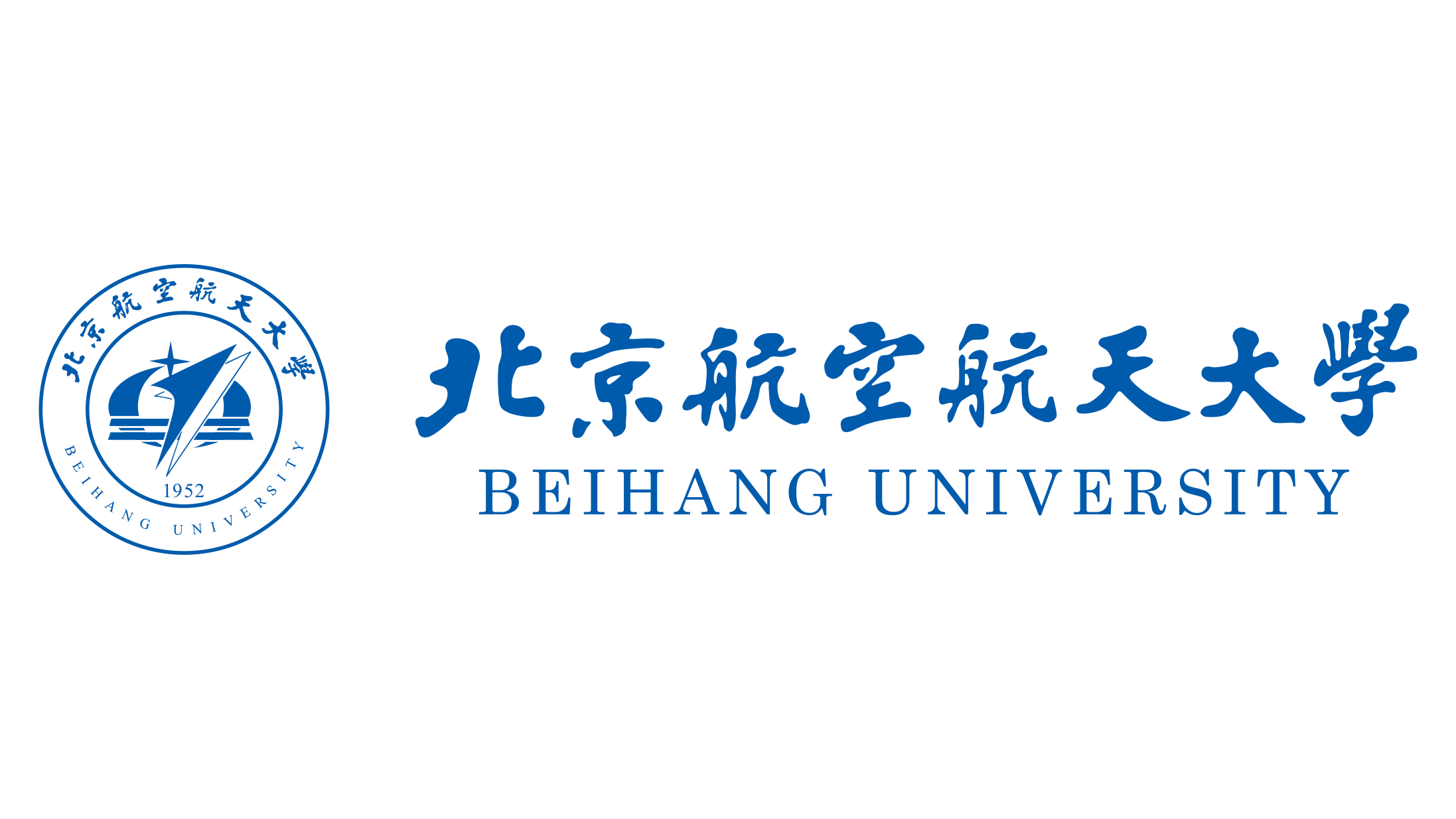
As environmental protection and the reduction of fossil fuel consumption are increasingly valued, the combustion process is required to be more efficient and cleaner. Therefore, obtaining key thermophysical parameters is crucial for combustion research and burner design. Traditional contact measurement technology will interfere with the combustion process.
Laser diagnostic technology, such as coherent anti-Stokes Raman scattering (CARS), is a widely used high-precision temperature measurement technology. Through the vibration or rotation resonance enhancement of gas molecules (usually N2), a beam of laser-like CARS signal light is generated through the four-wave mixing process. Vibration CARS can usually measure temperatures above 1000 K, and the single-point temperature measurement accuracy in the flame is 5%-10%. Before the engine ignition, even if it has reached maximum compression, its typical temperature is in the range of 400-600 K. At this time, the particle number distribution of the rotational state of N2 molecules is more sensitive to temperature. Through the rotation CARS technology, the single-point temperature measurement accuracy in the internal combustion engine can reach 5%-8%.
Laser induced fluorescence (LIF) is usually used for two-dimensional measurement of temperature field. The spatial resolution of LIF technology is usually less than 100um. However, CARS and LIF technologies obtain temperature by measuring the spectral distribution of signal intensity and light intensity respectively. They are easily affected by pumping light intensity disturbance and detector noise during measurement. Especially under high pressure, inelastic collisions between molecules reduce the effective fluorescence quantum yield, which greatly reduces the LIF signal intensity and is not conducive to signal interpretation.
Laser induced thermal grating spectroscopy (LITGS) technology perfectly solves the above problems.
In the experimental system, a continuous beam of detection light meets the Bragg scattering condition and can excite a coherent thermal grating signal in the cross region. After spatial and spectral filtering, this signal is detected by a photomultiplier tube and displayed and stored by a digital oscilloscope. This signal carries rich flow field information. Through frequency domain analysis, the temperature of the gas can be measured. The experimental results show that the temperature measured by the laser-induced thermal grating spectroscopy (LIGS) technology is in good agreement with the thermocouple temperature, showing a high measurement accuracy. In addition, the technology can also directly measure the gas sound velocity, and the measurement results are basically consistent with the theoretical curve within a certain temperature range, showing that the technology has high measurement accuracy and the ability to measure multiple parameters simultaneously.
Factors affecting the waveform of the thermal grating signal include pressure and gas component concentration. As the pressure increases, the signal intensity increases, the number of signal peaks also increases, and the signal decay rate decreases. Changes in gas component concentration will also affect the thermal grating signal waveform. Under low concentration and high pumping energy conditions, the generated electrostrictive signal can also be used for temperature measurement.
In general, the laser-induced grating temperature measurement system is a laser combustion diagnostic technology with broad application prospects, especially for temperature measurement in high-pressure environments.